Steel plates vs composite road plates
Wondering how we improved profitability, safety, efficiency and simplicity for our client, Balkan Plumbing? Learn more about how our plastic road plates and trench covers revolutionised this company’s operations.
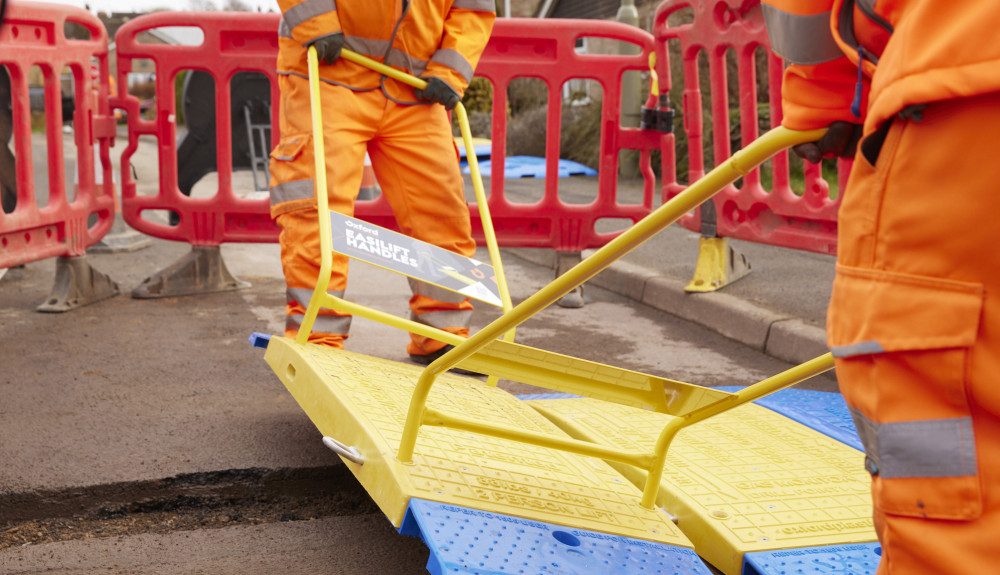
Oxford Plastics are proud to provide a detailed case study explaining how our work with Balkan Plumbing allowed them to significantly reduce unnecessary expenditure and seamlessly speed up their workflow.
About Balkan Plumbing
Balkan Plumbing is the largest sewer and water main specialists in New York, and has been for over 30 years. On a daily basis, Balkan Plumbing of NYC deploy multiple crews to install, repair and maintain water and sewer connections between the main lines and homes/buildings. The excavations require a temporary cover prior to the work being completed and the road surface restored.
Prior to the involvement of Oxford Plastics, Balkan used steel road plates delivered from their service yards to ‘safely’ cover a trench. However, they found this process itself came with its challenges:
- Additional workers required – due to the weight of the steel plates, they required at least two people to help lift these. This then, in turn, led to a reduction in profit due to the labour-power required.
- Heavy lifting equipment – specialised equipment was also required for the heavy lifting of these steel plates into place. The steel road plates would then also need to be anchored and edged into place to ensure a seamless transition from street to plate.
- Specialised transportation – transporting the steel road plates from yard to site also required specialised transport which, again, led to additional costs.
- Extra costs – not to mention the above costs of transport and workers, but inconveniencing the public also came with its costs – as well as opening up the potential for accidents to happen.
With numerous other disadvantages of using steel road plates, including noise pollution, street closures and reduction in profit due to labour-force required, something needed to be done.
That’s where Oxford Plastics – and our composite plastic road plates – came in, offering safety, savings and simplicity.
The process
Oxford Plastic’s plastic road plates and trench covers are able to support a crew of 4-6 workers. The team are dispatched into two trucks along with the equipment required to carry out an excavation. The excavation is carried out with a jack hammer and shovels, which is followed by the repair of the line and/or connection. Back filling and restoration of the asphalt roadway is then done. If the works require additional days, plating is needed to allow traffic access.
By using Oxford Plastics, the process itself has been simplified – meaning fewer workers are required, the set-up speed is faster and easier, the road plates are more secure and there’s less noise pollution. Learn more about the benefits of composite road plates from our guide.
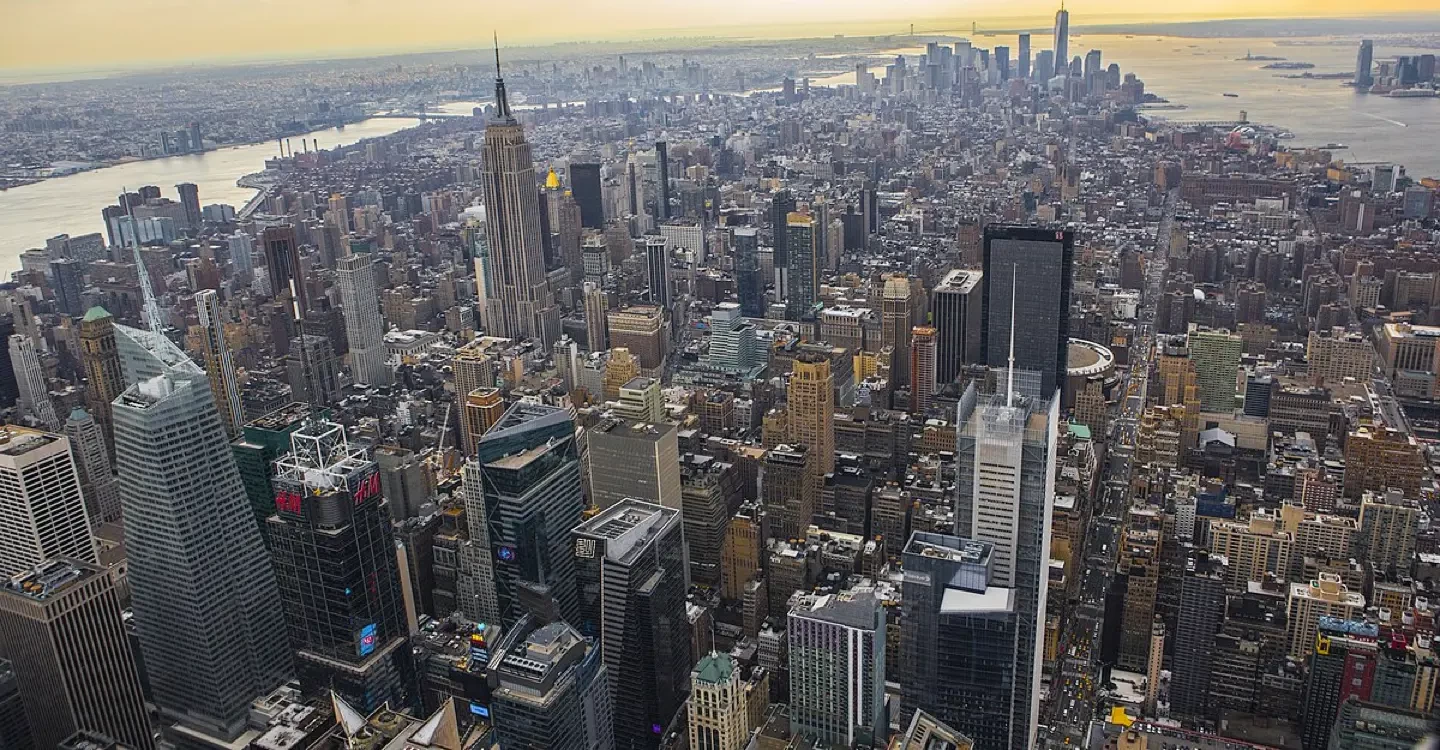
Balkan Plumbing
The largest sewer and water main specialist in New YorkOxford Plastics has made our operations more efficient, safer and more profitable.
Testimonial from Balkan’s CEO
We spoke to Dave Balkan, CEO of Joseph L Balkan Plumbing – who explained how Oxford Plastics has transformed their operations:
“Oxford Plastics has made our operations more efficient, safer and more profitable.
“Prior to using the composite plates, we’d sometimes have a 3-hour notice on a job – meaning we had to solve urgent problems using steel plates. This would mean we would need to open our facilities (which aren’t always open), move equipment and get to where the steel plates were stored.
“Then, loading up steel plates alone would need at least two guys to move them – and then we’d need to go out to a drop site and install them. All this would mean it would be unlikely that we’d meet the 3-hour deadline – which could result in a $1,200 summons.
“However, now we use Oxford Plastics plates, we are able to meet the deadline in less than an hour with no stress, no injury and no worry – knowing that everything will be easily taken care of.”
Benefits Balkan found using Oxford Plastics over steel plates
Cost
- Purchase price – reduction in overall expenditure on composite road plates as opposed to steel
- Compliance modifications – there would be no fines from applying anti-skid surfaces to plates, as the LowPro 23/05 has this moulded into the cover
- Maintenance – easier to install, transport and store than steel road plates
Efficiency
- Loading – more lightweight so easier to load, requiring less labour
- Transportation – no need for specialised transport, further reducing unnecessary costs
- Yard storage – easy to store and move around the yard or by hand
- Setting – using our LowPro technology, our products do not need to be anchored down unless specified in the risk assessment – meaning setting the road plates has never been easier
- Removal – as well as being easy to install, the removal of the road plates is also simple and quick – with no cold patch removal.
Want to know more about the differences between steel plates and composite road plates? Read our dedicated guide – or browse our range of LowPro road plates and trench covers online today.
More Case Studies
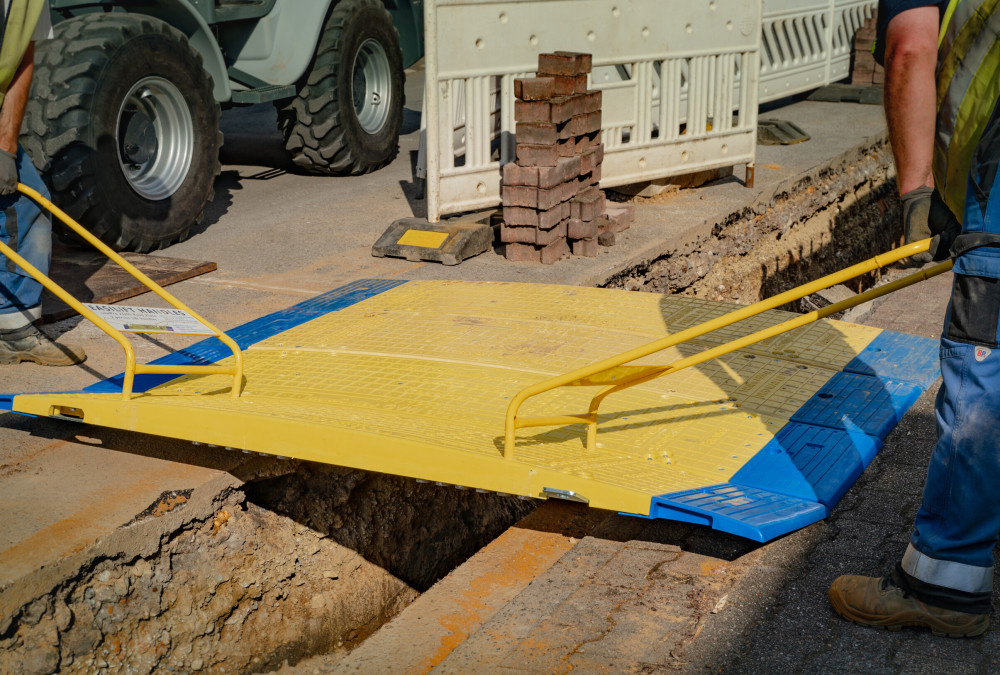
Supply Chain Sustainability School
Circularity and sustainability are central to Oxford Plastic's identity as a family-run SME. Our customer, Speedy, approached...
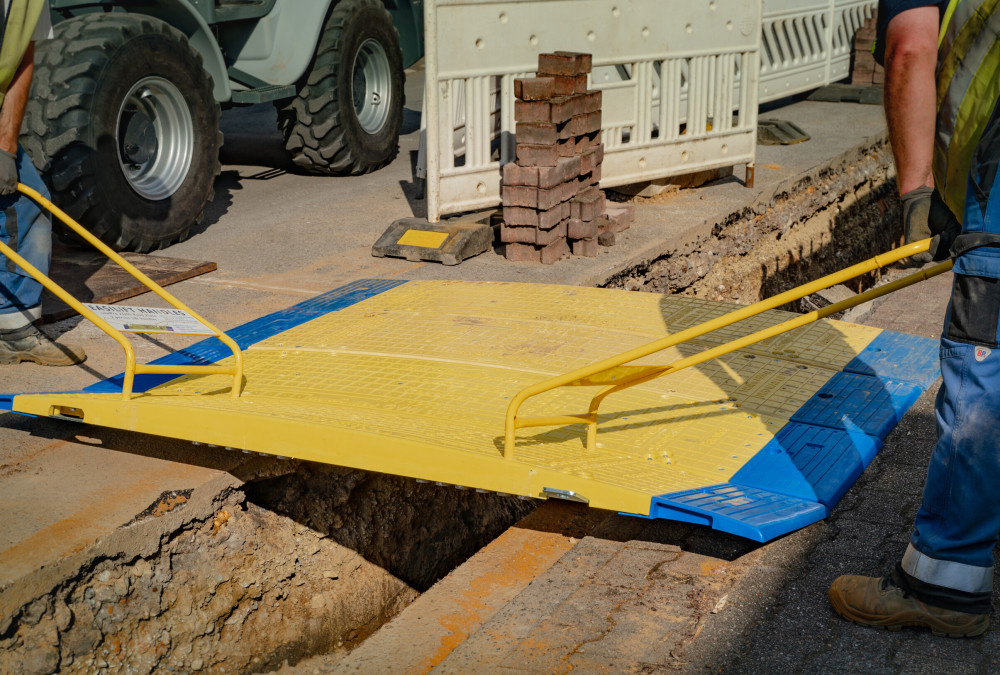
Supply Chain Sustainability School
Circularity and sustainability are central to Oxford Plastic's identity as a family-run SME. Our customer, Speedy, approached...
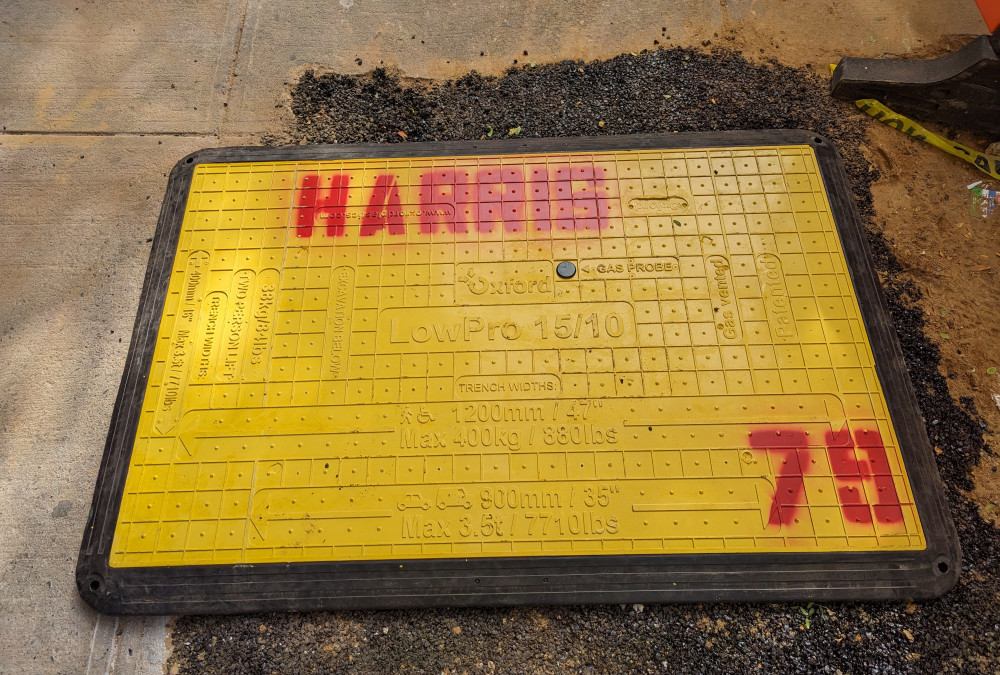
Harris Water Mains Improve Public Safety
4th Generation New York water and sewer contractor Harris Water Mains prioritizes public safety by making the switch to compo...