What is closed-loop manufacturing?
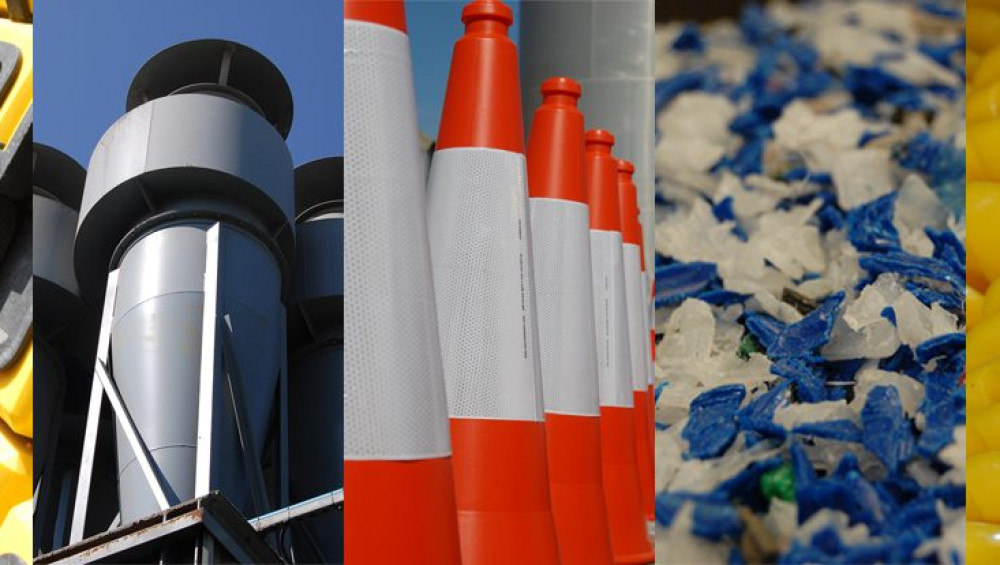
What is closed-loop manufacturing?
Closed-loop manufacturing is a process that reuses, recycles, and repurposes materials to reduce environmental impact. It aims to reduce waste and maximize the value of materials.
How does closed-loop manufacturing work?
Closed-loop manufacturing deals with the entire manufacturing process, from start to finish. It’s a circular process, which is also referred to as a circular economy. Closed-loop manufacturing should ensure that every step of the manufacturing process is considered for its environmental impact through its design, production, usage and end of life.
Closed-loop design
Products are designed with the entire lifecycle in mind. This includes considerations for;
- Durability of the product
- Right to repair
- Assembly and disassembly
- Recyclability
The product materials are intentionally chosen for their durable and recyclable qualities.
Our ethos is to design products that not only last a long time but include a modular design with spare parts empowering our customers with a right to repair.
The LowPro 15/10 is designed with durability in mind, with rubber edges that are protected from rough handling on site.
Closed-loop production
Closed-loop manufacturing utilizes production techniques that minimize wastage and energy usage. This can include advanced manufacturing techniques like 3D printing, artificial intelligence, and precision machining.
Here at Oxford Plastics, we save energy during the manufacturing process by using 75% recycled plastic in many of our products.
Closed-loop usage
Closed-loop manufacturing utilizes clever design that considers the carbon footprint of a product while it’s being used. This might be by making lighter products that take less energy to transport.
One of the ways we consider a circular economy for the users of our products is by eliminating the need for heavy machinery to install our products. A steel road plate's carbon footprint is increased by the need for machinery to install it safely, whereas the LowPro 23/05 can be installed easily by hand.
Closed-loop end-of-life
At the end of life, closed-loop products need to be processed so they can re-enter the supply chain and leave as little waste as possible. This can be achieved in the following ways.
- Collection and return
- Recycling
- Remanufacturing
We’re proud that all of our products can be returned to us to either be recycled or ethically disposed of. The Temporary Fence Weight not only is a safer and longer-lasting alternative to sandbags but is also truly closed loop, as it's made of recycled PVC and is 100% recyclable.
Why is closed-loop manufacturing important?
Closed-loop manufacturing has a significant impact on the environment but also has several other benefits including;
Cost savings
As closed-loop manufacturing focuses on a right to repair, customers will save money as replacing spare parts is more cost-effective than replacing the entire product. Reduced waste, disposal and manufacturing costs from raw materials ensure quality products at a lower cost.
Innovation
Closed-loop design is innovation first, resulting in products designed for a specific purpose that are easy to use in every stage of their lifecycle. By focusing on reducing waste and reusing and recycling materials closed-loop manufacturing often pioneers the latest manufacturing technology.
Environmental, Social and Governance
Closed-loop manufacturing can help users with their corporate responsibility. Reducing overall CO2 emissions within the supply chain, helping businesses to reach their net zero goals.
How can Oxford Plastics help?
Oxford Plastics is proud to use closed-loop manufacturing processes, 75% of our products are made from recycled plastics while 100% of our products can be recycled or recovered for energy.
Our products are long-lasting, repairable, and recyclable and we are dedicated to reducing carbon emissions in our supply chain.
Want to find out more about our commitment to sustainability? Read more. To find out more about our products, get in touch today.
Related News
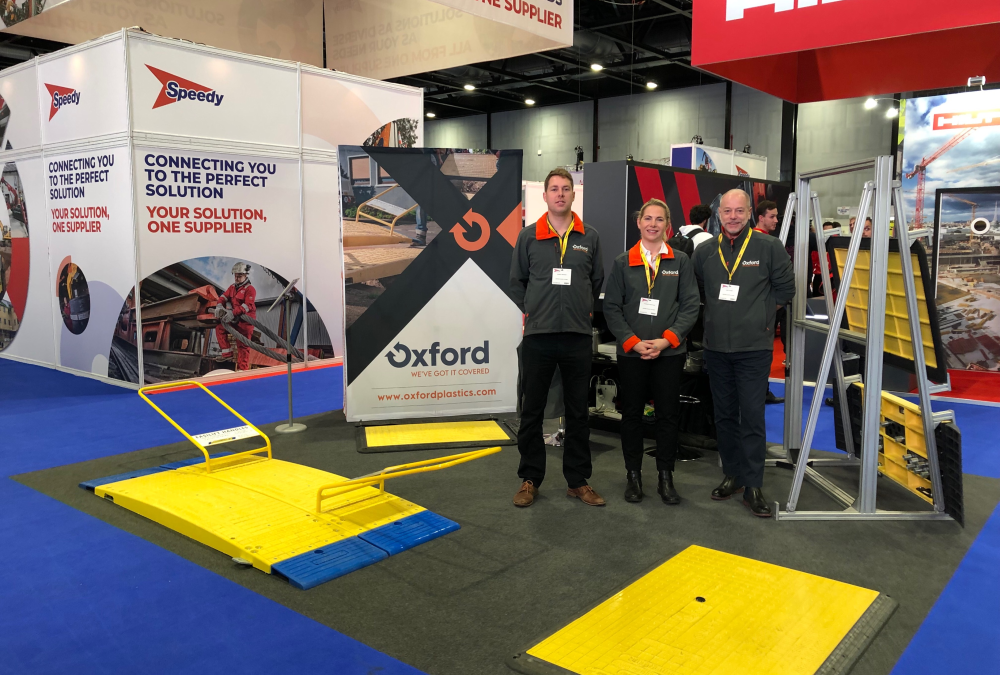
Health and Safety Calendar 2024 US
For over three decades, we have prioritized safety in all our innovations. That’s why we’ve compiled a list of es...
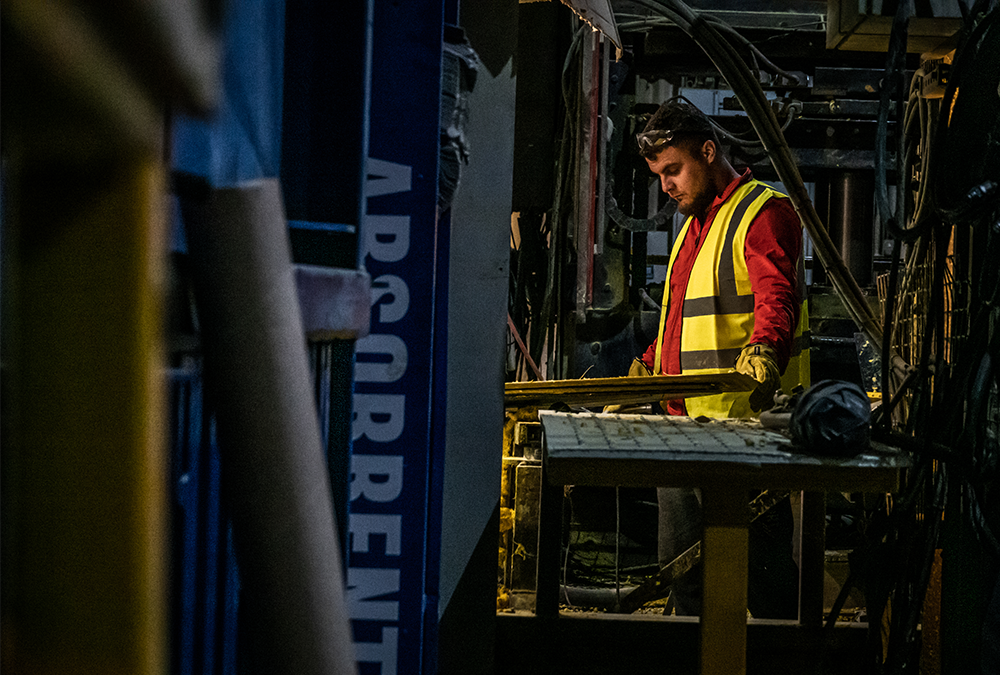
2023 a success for Oxford Plastics
As we enter 2024, as a business we’d like to reflect on the year we’ve had and look to our future goals. We&rsquo...
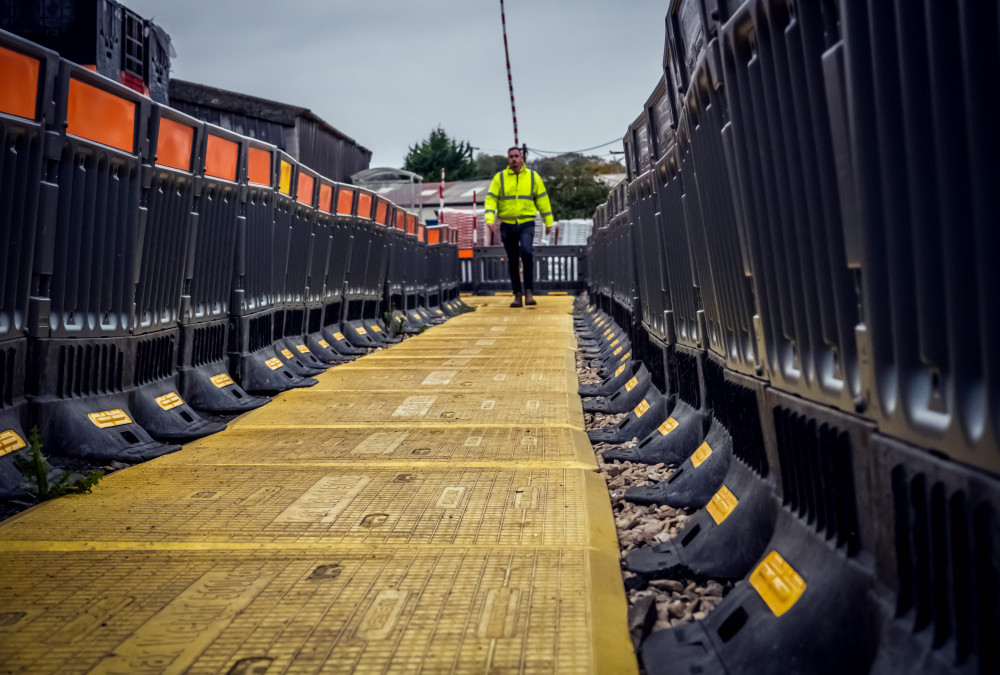
How can winter weather affect site safety
When it comes to site safety, each season can bring its hazards. From prolonged sun exposure in the summer to slippery fall c...